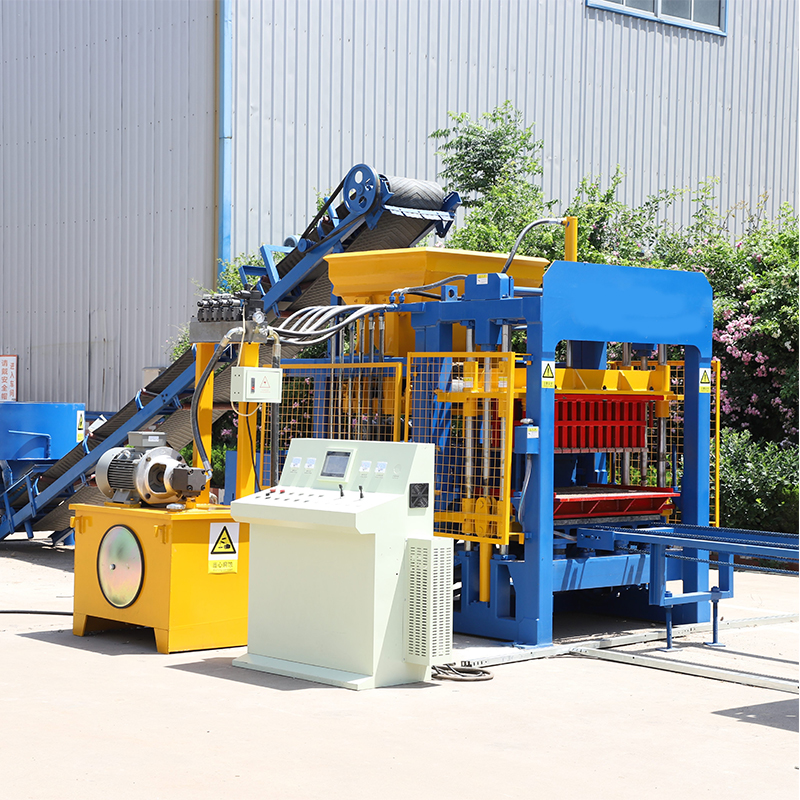
Image source :Aiweiblockmachine
Roles and Responsibilities of Workers in Block Making Factories
In a block making factory, various workers are involved in different stages of the production process, each with specific roles and responsibilities. The following is an overview of key roles within a block making factory:
- Factory Manager:
- Responsible for overall factory operations, including production planning, resource allocation, and quality control.
- Manages the production schedule, inventory, and distribution of finished products.
- Oversees maintenance and ensures compliance with safety and environmental regulations.
- Monitors financial performance and implements strategies to improve efficiency and profitability.
- Production Supervisor:
- Coordinates and supervises daily production activities.
- Assigns tasks to production team members and monitors their performance.
- Ensures adherence to production schedules, quality standards, and safety protocols.
- Collaborates with other departments to optimize production processes.
- Machine Operators:
- Operate and control the block making machines according to established procedures.
- Monitor machine performance, adjust settings as needed, and troubleshoot issues.
- Ensure the machines are running efficiently and producing blocks of the required quality.
- Quality Control Inspector:
- Conducts regular inspections of produced blocks to ensure they meet quality standards.
- Identifies defects, variations, or deviations from specifications and takes corrective actions.
- Keeps detailed records of inspection results and communicates findings to relevant personnel.
- Maintenance Technician:
- Performs routine maintenance and repairs on block making machines to prevent breakdowns.
- Conducts preventive maintenance tasks to ensure machines operate smoothly and efficiently.
- Responds to machine malfunctions promptly and troubleshoots technical issues.
- Material Handler:
- Receives, stores, and organizes raw materials like cement, aggregates, and additives.
- Prepares materials for production by measuring and mixing them according to specific formulas.
- Ensures an adequate supply of materials for continuous production.
- Palletizer and Packager:
- Organizes and stacks finished blocks on pallets according to established patterns.
- Labels and packages blocks for storage or transportation.
- Maintains records of the quantity, type, and condition of packed blocks.
- Logistics Coordinator:
- Coordinates transportation and distribution of finished blocks to customers or storage facilities.
- Ensures timely delivery and accurate documentation for shipments.
- Coordinates with shipping companies, drivers, and customers to optimize logistics.
- Administrative Staff:
- Handles administrative tasks, such as record-keeping, documentation, and reporting.
- Manages orders, invoices, and other paperwork related to production and sales.
- Provides support to the management team and facilitates communication within the factory.
- Health and Safety Officer:
- Enforces safety protocols and ensures compliance with occupational health and safety regulations.
- Conducts safety training sessions for workers and monitors workplace conditions to prevent accidents.
- Training and Development Specialist:
- Plans and conducts training programs for new hires and ongoing skill development of existing workers.
- Ensures that all workers are properly trained to operate machinery safely and efficiently.
- Environmental Officer:
- Ensures the factory’s compliance with environmental regulations.
- Monitors waste management practices and oversees initiatives to minimize environmental impact.
- Lab Technician:
- Conducts testing and analysis of raw materials and finished blocks to ensure they meet quality standards.
- Prepares and maintains records of test results, troubleshoots issues, and provides data for process improvement.
- Electrician:
- Installs, maintains, and repairs electrical systems and components of block making machines.
- Troubleshoots electrical issues, replaces faulty components, and ensures machines operate safely and efficiently.
- Mechanical Engineer:
- Designs and develops new block making machine models or improvements to existing machines.
- Collaborates with the production team to optimize machine performance and resolve mechanical issues.
- Sales and Marketing Team:
- Develops sales strategies and targets potential clients for block orders.
- Builds and maintains relationships with clients, provides product information, and negotiates contracts.
- Implements marketing initiatives to promote the factory’s products and services.
- Accounting and Finance Personnel:
- Manages financial transactions, prepares invoices, tracks payments, and manages accounts receivable and payable.
- Generates financial reports, analyzes budget variances, and ensures financial compliance.
- Human Resources Manager:
- Oversees recruitment, hiring, and onboarding of new staff members.
- Manages employee benefits, performance evaluations, and personnel development programs.
- Handles labor-related issues, maintains records, and ensures compliance with labor laws.
- Research and Development Specialist:
- Conducts research to explore innovations and improvements in block production processes.
- Tests new materials, techniques, and technologies to enhance product quality and efficiency.
- Inventory Controller:
- Manages inventory levels of raw materials, spare parts, and finished blocks.
- Monitors stock levels, initiates purchase orders, and maintains records to ensure uninterrupted production.
- Procurement Officer:
- Sources and negotiates with suppliers to secure cost-effective raw materials and equipment.
- Monitors market trends, evaluates supplier performance, and ensures timely deliveries.
- Lean Manufacturing Coordinator:
- Implements lean manufacturing principles to optimize production processes, minimize waste, and improve efficiency.
- Identifies opportunities for process improvement and leads continuous improvement initiatives.
- Community Relations Liaison:
- Establishes positive relationships with the local community, addressing concerns and maintaining a harmonious presence.
- Communicates the factory’s commitment to environmental and social responsibility.
- Safety Committee Members:
- Collaborate with health and safety officers to identify potential hazards and develop safety protocols.
- Conduct regular safety inspections, organize safety training, and promote a culture of workplace safety.
Remember that the specific roles and their responsibilities can vary based on the organizational structure, the size of the factory, and the nature of the block making operations. Effective teamwork, communication, and a shared commitment to quality and efficiency are essential for the overall success of a block making factory.