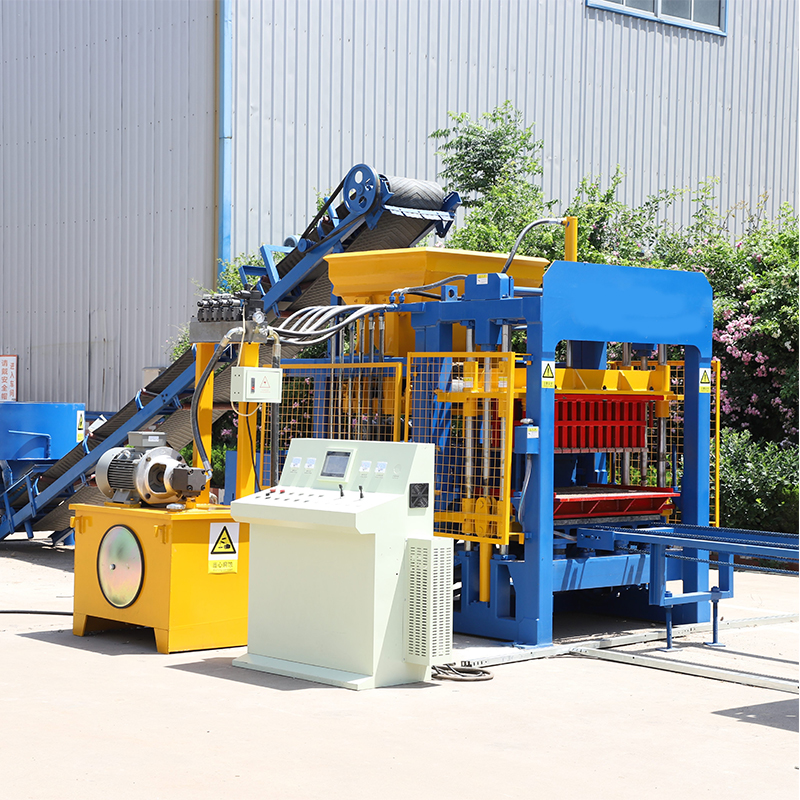
Image source :Aiweiblockmachine
Training and Skill Development for Block Making Machine Workers
In the realm of modern manufacturing, the success and efficiency of any operation are greatly dependent on the skills and expertise of its workforce. This principle holds true in the context of block making factories, where the quality, consistency, and productivity of the produced blocks hinge on the proficiency of the workers operating the block making machines. To meet the demands of a competitive industry and ensure the optimal performance of the factory, investing in comprehensive training and skill development programs for block making machine workers is not just a necessity but a strategic imperative.
The Importance of Training and Skill Development
In the dynamic and evolving field of manufacturing, embracing technological advancements and best practices is essential to remain competitive and meet customer expectations. The introduction of automated and semi-automated block making machines has revolutionized the production process, allowing for increased efficiency, precision, and consistency. However, these advancements also mean that workers need to acquire a new set of skills to effectively operate and maintain these machines.
Training and skill development programs are not only a means to bridge this skills gap but also a vehicle to achieve a range of benefits for both workers and the organization:
1. Enhanced Productivity: Proficient workers can operate machines efficiently, reducing downtime and maximizing production output.
2. Improved Quality: Proper training ensures that workers understand quality standards and can consistently produce high-quality blocks that meet specifications.
3. Safety: Training emphasizes safety protocols, reducing the risk of accidents and injuries in the workplace.
4. Employee Morale: Skill development shows that the organization is invested in its workers’ growth, boosting morale and job satisfaction.
5. Adaptability: Continuous learning equips workers with the ability to adapt to new technologies and changes in the production process.
6. Reduced Costs: Skilled workers can identify and troubleshoot issues, minimizing maintenance costs and preventing production bottlenecks.
7. Innovation: Well-trained employees are more likely to contribute innovative ideas for process improvement.
Components of Effective Training and Skill Development Programs
To ensure the effectiveness of training and skill development programs for block making machine workers, several key components should be considered:
1. Needs Assessment: Begin by assessing the specific training needs of the workforce. Identify gaps in skills, knowledge, and understanding that hinder optimal machine operation.
2. Customization: Tailor the training programs to the needs and experience levels of the workers. Differentiate between beginners and experienced operators.
3. Practical Training: Blend theoretical knowledge with hands-on, practical training. Allow workers to operate the machines under supervision to reinforce learning.
4. Safety Training: Emphasize safety protocols, including proper machine operation, emergency procedures, and the use of personal protective equipment.
5. Equipment Familiarization: Provide a comprehensive understanding of the block making machines’ components, functions, and maintenance requirements.
6. Quality Control: Train workers in quality assurance techniques to ensure that blocks meet required specifications and pass inspections.
7. Maintenance Skills: Equip workers with basic maintenance skills to troubleshoot minor issues and perform routine maintenance tasks.
8. Communication: Teach effective communication skills, as collaboration and clear communication are crucial in a factory setting.
9. Continuous Learning: Offer ongoing training and skill development opportunities to keep workers updated with the latest industry trends and technological advancements.
10. Assessments and Feedback: Regularly evaluate trainees’ progress through assessments and provide constructive feedback for improvement.
Methods of Training
Training and skill development for block making machine workers can be delivered through various methods, each with its own advantages:
1. On-the-Job Training: Workers learn while performing their regular duties, under the guidance of experienced operators or trainers.
2. Workshops and Seminars: Group training sessions led by experts provide theoretical and practical insights into machine operation and maintenance.
3. E-Learning: Online platforms offer the flexibility for workers to access training modules at their own pace.
4. Simulation: Simulators replicate real-world machine operations, allowing trainees to practice in a controlled environment.
5. Mentorship Programs: Pair new workers with experienced mentors who guide them through the learning process.
Challenges and Mitigation
Implementing effective training and skill development programs comes with its own set of challenges:
1. Time Constraints: Balancing training with production demands can be challenging. Develop a schedule that minimizes disruption.
2. Resistance to Change: Workers might resist new methods. Clearly communicate the benefits and involve them in the training process.
3. Resource Constraints: Limited resources can impact the scope and quality of training. Prioritize essential skills and seek cost-effective solutions.
4. Training Sustainability: Ensure that training efforts are ongoing to keep up with industry changes and maintain a skilled workforce.
Case Study: “SkillBlock Industries”
Scenario: SkillBlock Industries, a medium-sized block making factory, recognized the need to enhance the skills of its workforce to stay competitive.
Approach: The company implemented a comprehensive training program that encompassed both theoretical knowledge and practical hands-on training. The program covered machine operation, maintenance, safety protocols, and quality control.
Outcome: After the training program, SkillBlock Industries observed a significant reduction in machine-related errors and maintenance downtime. The quality of the blocks improved, leading to higher customer satisfaction. Workers reported feeling more confident in their roles and appreciated the company’s investment in their professional development.
In the realm of modern manufacturing, the success and efficiency of any operation are greatly dependent on the skills and expertise of its workforce. This principle holds true in the context of block making factories, where the quality, consistency, and productivity of the produced blocks hinge on the proficiency of the workers operating the block making machines. To meet the demands of a competitive industry and ensure the optimal performance of the factory, investing in comprehensive training and skill development programs for block making machine workers is not just a necessity but a strategic imperative.
The Importance of Training and Skill Development
In the dynamic and evolving field of manufacturing, embracing technological advancements and best practices is essential to remain competitive and meet customer expectations. The introduction of automated and semi-automated block making machines has revolutionized the production process, allowing for increased efficiency, precision, and consistency. However, these advancements also mean that workers need to acquire a new set of skills to effectively operate and maintain these machines.
Training and skill development programs are not only a means to bridge this skills gap but also a vehicle to achieve a range of benefits for both workers and the organization:
1. Enhanced Productivity: Proficient workers can operate machines efficiently, reducing downtime and maximizing production output.
2. Improved Quality: Proper training ensures that workers understand quality standards and can consistently produce high-quality blocks that meet specifications.
3. Safety: Training emphasizes safety protocols, reducing the risk of accidents and injuries in the workplace.
4. Employee Morale: Skill development shows that the organization is invested in its workers’ growth, boosting morale and job satisfaction.
5. Adaptability: Continuous learning equips workers with the ability to adapt to new technologies and changes in the production process.
6. Reduced Costs: Skilled workers can identify and troubleshoot issues, minimizing maintenance costs and preventing production bottlenecks.
7. Innovation: Well-trained employees are more likely to contribute innovative ideas for process improvement.
Components of Effective Training and Skill Development Programs
To ensure the effectiveness of training and skill development programs for block making machine workers, several key components should be considered:
1. Needs Assessment: Begin by assessing the specific training needs of the workforce. Identify gaps in skills, knowledge, and understanding that hinder optimal machine operation.
2. Customization: Tailor the training programs to the needs and experience levels of the workers. Differentiate between beginners and experienced operators.
3. Practical Training: Blend theoretical knowledge with hands-on, practical training. Allow workers to operate the machines under supervision to reinforce learning.
4. Safety Training: Emphasize safety protocols, including proper machine operation, emergency procedures, and the use of personal protective equipment.
5. Equipment Familiarization: Provide a comprehensive understanding of the block making machines’ components, functions, and maintenance requirements.
6. Quality Control: Train workers in quality assurance techniques to ensure that blocks meet required specifications and pass inspections.
7. Maintenance Skills: Equip workers with basic maintenance skills to troubleshoot minor issues and perform routine maintenance tasks.
8. Communication: Teach effective communication skills, as collaboration and clear communication are crucial in a factory setting.
9. Continuous Learning: Offer ongoing training and skill development opportunities to keep workers updated with the latest industry trends and technological advancements.
10. Assessments and Feedback: Regularly evaluate trainees’ progress through assessments and provide constructive feedback for improvement.
Methods of Training
Training and skill development for block making machine workers can be delivered through various methods, each with its own advantages:
1. On-the-Job Training: Workers learn while performing their regular duties, under the guidance of experienced operators or trainers.
2. Workshops and Seminars: Group training sessions led by experts provide theoretical and practical insights into machine operation and maintenance.
3. E-Learning: Online platforms offer the flexibility for workers to access training modules at their own pace.
4. Simulation: Simulators replicate real-world machine operations, allowing trainees to practice in a controlled environment.
5. Mentorship Programs: Pair new workers with experienced mentors who guide them through the learning process.
Challenges and Mitigation
Implementing effective training and skill development programs comes with its own set of challenges:
1. Time Constraints: Balancing training with production demands can be challenging. Develop a schedule that minimizes disruption.
2. Resistance to Change: Workers might resist new methods. Clearly communicate the benefits and involve them in the training process.
3. Resource Constraints: Limited resources can impact the scope and quality of training. Prioritize essential skills and seek cost-effective solutions.
4. Training Sustainability: Ensure that training efforts are ongoing to keep up with industry changes and maintain a skilled workforce.
Case Study: “SkillBlock Industries”
Scenario: SkillBlock Industries, a medium-sized block making factory, recognized the need to enhance the skills of its workforce to stay competitive.
Approach: The company implemented a comprehensive training program that encompassed both theoretical knowledge and practical hands-on training. The program covered machine operation, maintenance, safety protocols, and quality control.
Outcome: After the training program, SkillBlock Industries observed a significant reduction in machine-related errors and maintenance downtime. The quality of the blocks improved, leading to higher customer satisfaction. Workers reported feeling more confident in their roles and appreciated the company’s investment in their professional development.
Conclusion
In the rapidly evolving landscape of manufacturing, investing in training and skill development for block making machine workers is an imperative strategy. A skilled workforce is not only an asset but a catalyst for increased efficiency, innovation, and competitiveness. By providing workers with the knowledge and tools to operate and maintain advanced machines, organizations can ensure high-quality production, workplace safety, and overall success in the block making industry.