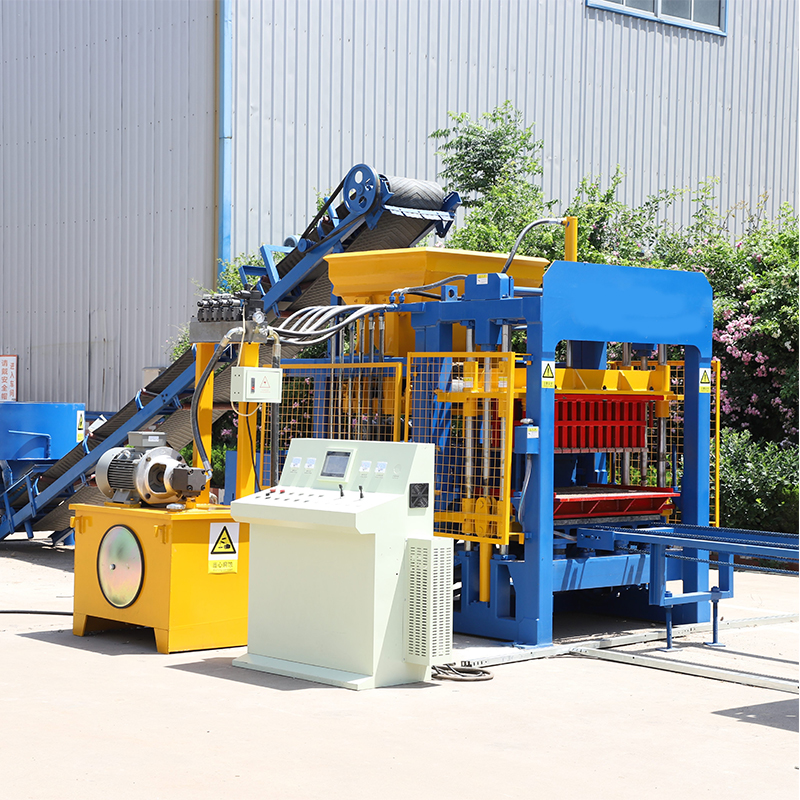
Image source :Aiweiblockmachine
Worker Safety and Occupational Health in Block Making Factories
In the bustling environment of block making factories, where the clatter of machinery and the hum of production fill the air, ensuring the safety and health of workers is of paramount importance. The manufacturing process, which involves heavy machinery, raw materials, and various processes, can pose potential risks if proper safety measures and occupational health protocols are not in place. Addressing these concerns is not just a moral obligation but also a legal and operational imperative. In this article, we delve into the key aspects of worker safety and occupational health in block making factories.
Understanding the Risks
Block making factories present a range of potential risks to worker safety and health. Some of these risks include:
1. Machinery Hazards: The operation of block making machines involves moving parts, conveyor belts, and other mechanisms that can lead to entanglement, crushing, or impact injuries.
2. Chemical Exposure: Workers may be exposed to dust, cement particles, and other airborne pollutants during the mixing and production process, leading to respiratory issues and skin conditions.
3. Heavy Lifting: Handling raw materials, molds, and finished blocks can result in musculoskeletal injuries if proper lifting techniques are not practiced.
4. Noise and Vibration: The noise generated by machinery and the vibrations from equipment can contribute to hearing loss and other health issues over time.
5. Slips, Trips, and Falls: The factory environment may have uneven surfaces, spills, and debris that can lead to slips, trips, and falls.
6. Electrical Hazards: Electrical systems in factories can pose risks if not properly maintained, leading to shocks or even electrical fires.
Safety Measures and Protocols
To ensure worker safety and promote occupational health, block making factories should implement a comprehensive set of safety measures and protocols:
1. Employee Training: Provide thorough training to workers on machine operation, safety protocols, emergency procedures, and proper equipment usage.
2. Personal Protective Equipment (PPE): Mandate the use of appropriate PPE, such as helmets, safety goggles, gloves, masks, and hearing protection, depending on the tasks performed.
3. Machine Guards: Install machine guards to prevent contact with moving parts and to reduce the risk of entanglement or crushing injuries.
4. Ventilation and Dust Control: Implement effective ventilation systems and dust control measures to minimize exposure to airborne particles and pollutants.
5. Ergonomics: Design workstations and tasks to minimize strain on the body, providing ergonomic tools and equipment to reduce the risk of musculoskeletal injuries.
6. Noise Reduction: Install noise barriers, isolation pads, and other measures to mitigate noise levels and protect workers’ hearing.
7. Regular Maintenance: Conduct routine inspections and maintenance of machinery to ensure that equipment is functioning properly and safely.
8. Hazardous Materials Handling: Implement proper storage, labeling, and handling procedures for chemicals and hazardous materials, and provide workers with guidelines for safe use.
9. Housekeeping: Maintain a clean and organized workspace to reduce the risk of slips, trips, and falls.
10. Emergency Preparedness: Have well-defined emergency response plans in place, including fire drills, evacuation procedures, and first aid training.
Worker Health and Well-being
Ensuring the health and well-being of workers extends beyond physical safety and includes aspects of mental and emotional health:
1. Work-Life Balance: Implement reasonable work hours and breaks to prevent fatigue and burnout.
2. Mental Health Support: Provide resources and counseling services to address stress and mental health concerns.
3. Hydration and Nutrition: Encourage workers to stay hydrated and provide access to clean drinking water. Promote healthy eating habits.
4. Work Environment: Create a supportive work environment that encourages communication and collaboration among workers.
Case Study: “SafeBlock Manufacturing”
Scenario: SafeBlock Manufacturing is a medium-sized block making factory that prioritizes worker safety and health.
Approach: The company invested in modern machinery with enhanced safety features, provided rigorous training for workers, and implemented a safety committee to oversee workplace safety measures.
Outcome: The safety committee identified potential hazards and implemented measures to address them. The company observed a significant reduction in workplace accidents, leading to improved morale among workers. SafeBlock Manufacturing’s commitment to worker safety also positively impacted its reputation and customer trust.
In the bustling environment of block making factories, where the clatter of machinery and the hum of production fill the air, ensuring the safety and health of workers is of paramount importance. The manufacturing process, which involves heavy machinery, raw materials, and various processes, can pose potential risks if proper safety measures and occupational health protocols are not in place. Addressing these concerns is not just a moral obligation but also a legal and operational imperative. In this article, we delve into the key aspects of worker safety and occupational health in block making factories.
Understanding the Risks
Block making factories present a range of potential risks to worker safety and health. Some of these risks include:
1. Machinery Hazards: The operation of block making machines involves moving parts, conveyor belts, and other mechanisms that can lead to entanglement, crushing, or impact injuries.
2. Chemical Exposure: Workers may be exposed to dust, cement particles, and other airborne pollutants during the mixing and production process, leading to respiratory issues and skin conditions.
3. Heavy Lifting: Handling raw materials, molds, and finished blocks can result in musculoskeletal injuries if proper lifting techniques are not practiced.
4. Noise and Vibration: The noise generated by machinery and the vibrations from equipment can contribute to hearing loss and other health issues over time.
5. Slips, Trips, and Falls: The factory environment may have uneven surfaces, spills, and debris that can lead to slips, trips, and falls.
6. Electrical Hazards: Electrical systems in factories can pose risks if not properly maintained, leading to shocks or even electrical fires.
Safety Measures and Protocols
To ensure worker safety and promote occupational health, block making factories should implement a comprehensive set of safety measures and protocols:
1. Employee Training: Provide thorough training to workers on machine operation, safety protocols, emergency procedures, and proper equipment usage.
2. Personal Protective Equipment (PPE): Mandate the use of appropriate PPE, such as helmets, safety goggles, gloves, masks, and hearing protection, depending on the tasks performed.
3. Machine Guards: Install machine guards to prevent contact with moving parts and to reduce the risk of entanglement or crushing injuries.
4. Ventilation and Dust Control: Implement effective ventilation systems and dust control measures to minimize exposure to airborne particles and pollutants.
5. Ergonomics: Design workstations and tasks to minimize strain on the body, providing ergonomic tools and equipment to reduce the risk of musculoskeletal injuries.
6. Noise Reduction: Install noise barriers, isolation pads, and other measures to mitigate noise levels and protect workers’ hearing.
7. Regular Maintenance: Conduct routine inspections and maintenance of machinery to ensure that equipment is functioning properly and safely.
8. Hazardous Materials Handling: Implement proper storage, labeling, and handling procedures for chemicals and hazardous materials, and provide workers with guidelines for safe use.
9. Housekeeping: Maintain a clean and organized workspace to reduce the risk of slips, trips, and falls.
10. Emergency Preparedness: Have well-defined emergency response plans in place, including fire drills, evacuation procedures, and first aid training.
Worker Health and Well-being
Ensuring the health and well-being of workers extends beyond physical safety and includes aspects of mental and emotional health:
1. Work-Life Balance: Implement reasonable work hours and breaks to prevent fatigue and burnout.
2. Mental Health Support: Provide resources and counseling services to address stress and mental health concerns.
3. Hydration and Nutrition: Encourage workers to stay hydrated and provide access to clean drinking water. Promote healthy eating habits.
4. Work Environment: Create a supportive work environment that encourages communication and collaboration among workers.
Case Study: “SafeBlock Manufacturing”
Scenario: SafeBlock Manufacturing is a medium-sized block making factory that prioritizes worker safety and health.
Approach: The company invested in modern machinery with enhanced safety features, provided rigorous training for workers, and implemented a safety committee to oversee workplace safety measures.
Outcome: The safety committee identified potential hazards and implemented measures to address them. The company observed a significant reduction in workplace accidents, leading to improved morale among workers. SafeBlock Manufacturing’s commitment to worker safety also positively impacted its reputation and customer trust.
Conclusion
Worker safety and occupational health are not just legal requirements; they are crucial elements of a responsible and ethical approach to operating a block making factory. By implementing comprehensive safety measures, providing proper training, and promoting worker well-being, factories can create a culture of safety, enhance productivity, reduce accidents, and ultimately ensure the health and livelihood of their workforce. A safe and healthy workplace is an investment in both the present and the future success of the factory and its workers.